FLEXIBLE advantages
Unshaped Refractory Materials
Unshaped refractory materials often referred to as monolithic refractories offer numerous advantages n high-temperature applications. Applied on-site, they form a continuous, seamless lining, adapting perfectly to the required shape and size. Different installation techniques such as casting, ramming, shot-creting, and gunning with respectively without molds enable automation of the lining procedure – a clear ergonomic advantage when compared to manually operated bricking.
Unlike refractory bricks, monolithic linings develop their properties when exposed to high temperatures during use. That often gives them higher flexibility for reducing thermal stresses in the lining because high temperature sintering only occurs at the hot face of the lining. A lower strength level in deeper layers enables a mechanical cleaning of the hot face after a defined period of use and subsequent relining with a fresh layer on the remaining material. Such relining techniques lead to an overall lower specific refractory consumption and a more sustainable lining approach.
The potential combinations of unshaped refractory materials are very diverse, thanks to the vast selection of aggregates and bonding agents. The choice of installation method — be it casting, gunning, or ramming — significantly influences the product's development, effectiveness, and service life.
The higher complexity of properties development during use of unshaped refractory materials requires a thorough understanding of the intended operating conditions to ensure the selection of the correct materials for optimal performance.
At Almatis, our expertise in this field, coupled with a comprehensive range of high alumina raw materials, enables us to offer solutions that meet the distinct requirements of each application. This ensures durability and efficiency in various high-temperature environments.
Refractories Product Line
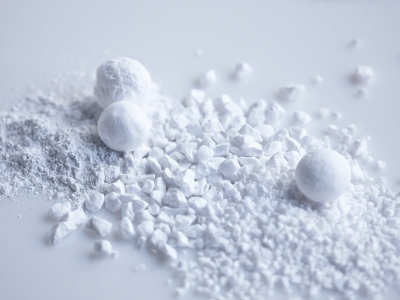
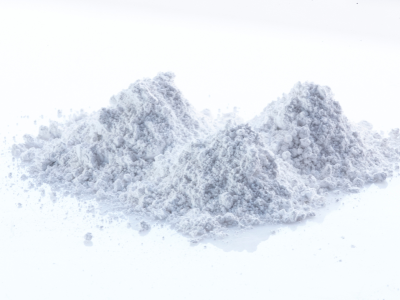
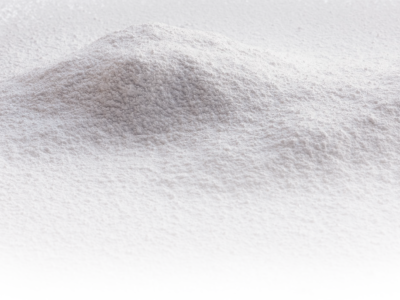
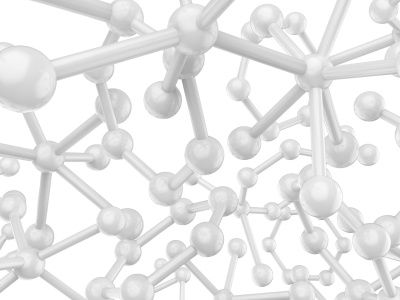
