We are in the business of pursuing progress.
Shaping the Alumina Landscape
With over a century of alumina expertise, Almatis is the world leader in developing, producing and delivering premium alumina and alumina-based products. Operating across fourteen sales, research and manufacturing hubs worldwide, we pride ourselves on a fully integrated approach, ensuring industry-leading service and support.
We pioneer advanced technologies and continuous improvement programs, solidifying Almatis as the quality benchmark. Our strong customer partnerships cultivate innovative solutions that support growth in all regions of the world.
Creating Exceptional Product Solutions
We offer the industry's most comprehensive alumina portfolio. Across our core markets —refractories, ceramics, and polishing— we redefine convenience with a one-stop shopping experience, continuously expanding our contribution to meet evolving customer and market demands.
Our expansive product line includes:
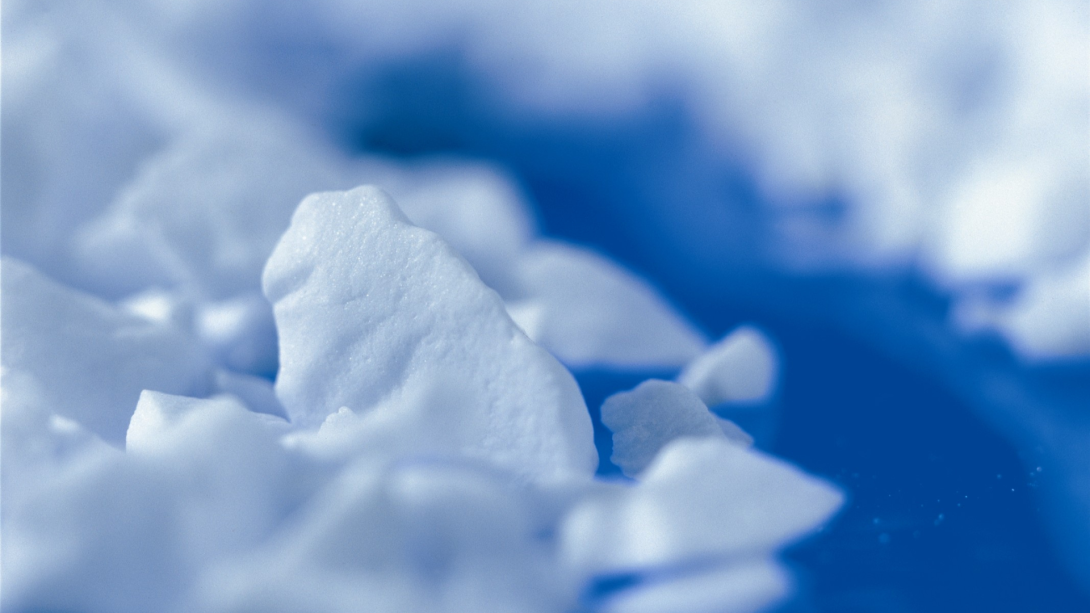
- Tabular aluminas
- Calcined and reactive aluminas
- Polishing aluminas
- Calcium aluminate cements
- Alphabond 300
- Dispersing aluminas
- Alumina and magnesia-rich spinels
- Calcium hexa-aluminate SLA 92
Setting a Standard of Excellence
At Almatis, we aim to deliver real value for our customers, empowering their performance and elevating their businesses with our stellar products and services. Our commitment to manufacturing excellence and quality shines across our entire product spectrum within each of our eight strategically positioned production sites.
Our global customer service and supply chain teams, armed with boundless expertise earned over 100 years of alumina research and investment, cater to our customers individually and meet their unique requirements, offering the impeccable level of service we are known for.
Driving Growth through Innovation
With an established legacy of research and development, we can anticipate the needs of the future, leading the market with new uses of alumina and investing relentlessly in process and product breakthroughs.
Our pledge to share our extensive alumina knowledge with our celebrated customers ensures they too can become industry leaders.
Our customers become clients; they are the focal point of our consistent dedication and the force that keeps us relentlessly pulling toward improvement and innovation.
Alumina, commonly recognized as the feed for the production of aluminum metal production, extends its versatility by undergoing further refinement to yield a spectrum of specialty aluminas created for diverse, non-metallic applications.
Bauxite is the raw material for the production of aluminum trihydrate and ultimately alumina or aluminum oxide. Depending on the quality of the ore, anywhere between two to four tons of bauxite is required for each ton of alumina produced.
The progression from alumina to specialty aluminas involves key stages based on the intended application:
- Grinding
- Purification
- Agglomeration
- Sintering/Calcination
- Crushing
- Sieving
The unique physical and chemical properties of this specialty or synthetic aluminum oxide make it an indispensable raw material across multiple market applications. The main considerations for selecting specialty aluminas include chemical purity —predominantly the level of soda— and the primary crystal size.
Known for its exceptional properties, aluminum oxide exhibits outstanding heat resistance with its fusion point of 2050°C (3725°F), classifying it as an excellent thermal and electrical insulator.
Its crystalline form, known as corundum, possesses extreme hardness, rendering it suitable for abrasives and as a component in cutting tools. To put things into context, corundum is the second hardest material after the diamond. Additionally, aluminum oxide adds exceptional mechanical strength, offers impressive resistance to corrosion and wear, and is a nontoxic material.
Refractories
Refractories are specialized materials that maintain strength at high temperatures, commonly employed in making crucibles and linings for furnaces, kilns, and incinerators. The refractory material is the surface in the vessel or furnace that comes in direct contact with the extremely hot metal, glass or other material that is being processed. As a result, refractories require strength at elevated temperatures, resistance to thermal shock, chemical inertness, and low thermal conductivities and coefficients of expansion.
Refractories must be chosen based on the conditions that they will face in service. Alumina, an aluminum oxide, stands out as an important refractory material extensively used in a variety of industries such as steel, cement, petrochemicals, non-ferrous metal production and glass manufacturing. Its widespread adoption is attributed to its superior mechanical strength and thermal shock resistance under the extreme temperatures used in materials production.
Ceramics
Ceramics are inorganic, non-metallic materials formed through heat action.
Historically, the most important ceramics were mined clays, used for pottery, bricks and tiles, as well as in cement and glass production. Over time, alumina and other advanced ceramic materials have significantly expanded ceramic applications.
In the present day, technical ceramics play an important role in our lives. A large number of our household appliances could not function without ceramic insulating elements. Insulators, fuses, and circuit-breaker elements are made from technical ceramics to ensure a safe and reliable power supply. Across the electronics fields, ceramic substrates and components find extensive use in various devices and subassemblies. Meanwhile, ceramic seals and regulator discs contribute to wear-free operation and effective sealing in valves and household water taps.
While these examples illustrate the importance of technical ceramics, it is worth noting that these components, integrated into larger units, equipment and vehicles, often remain hidden, even though we heavily rely on them for everyday solutions.
Polishing
Polishing is the process of creating a sleek surface, often to achieve a shiny and appealing look. As an essential abrasive material, Alumina is extensively used in various polishing applications, from metal surfaces like motorbikes or cooking pots to medical instruments, where a polished surface eliminates potential bacterial growth areas. Household cleaners target stains on materials like porcelain, while automotive polishes restore original luster. Stones undergo polishing to enhance natural beauty, and teeth are polished for a whiter appearance.
In fulfilling these diverse needs, the widespread use and value of Polishing Aluminas are evident. With a Mohs' hardness of 9, second only to diamonds, alumina efficiently polishes softer materials.